Three-roll rolling
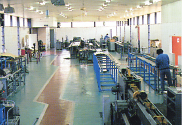
0.001mm:
Processing accuracy for inner and outer diameters is 0.001 mm. these diameters can be adjusted by 0.01mm unit.
rEDUCING DEVIATIONS:
Processing reduces deviations in wall thickness.
IMPROVING SURFACE ROUGHNESS:
Lower frictional resistance improves surface roughness.
IMPROVING MECHANICAL STRENGTH:
Processing enables high reduction, ensuring finer grain & improved mechanical strength.
Sample:SUS316L
Rz=0.6μm Rz JIS=0.6μm
Sample:SUS304TP
Rz=0.6μm Rz JIS=0.6μm
more than 50%
This process can accept more than 50% reduction at cross-section.
suitable cross-section
By controlling the tool set, it is possible to obtain a suitable cross-section.
15 meters long
This rolling machine can be produced in the tube 15 meters
long
OUTER DIAMETER
Inner Diameter
wall thickness
Three-roll cold processing ensures high accuracy, dimensional tolerance, and surface roughness not attainable in drawing processes (drawing and cold drawing). Other advantages include the following, making effective use of materials.
1. Tubing using extra-short cutting rods
Tohsei Kokan Cutting materials from rods are used if materials for tubes including special metals are not available. Three-roll cold rolling enables tube processing regardless of quantity if short rods (20 mmL or more) are available.
Examples include:
♦ 22 mm diameter × 250 mm L → 4 mm diameter × 0.25 mm t × 25,000 mm L
♦ 20 mm diameter × 20 mm L → 5 mm diameter × 0.5 mm t × 600 mm L
Any material can be used except for those with small elongation. This is because of metal characteristics. Examples: tungsten, molybdenum, berylium.
2. Extra-long tube stretching
In drawing, it is not possible to make products exceeding the length of drawing equipment. Longer products become distorted during drawing, causing problems in dimensional accuracy. Three-roll rolling enables rolling of extra-long tubes of 12 M or more while ensuring stable dimensional accuracy, thanks to the special features of this process.
Note:
1. Cost rises due to expensive tools and slow processing.
2. Heat treatment in a bright environment is required to maintain high-accuracy surface roughness during heat treatment. Manufacturing is not possible if such heat treatment in a bright environment is not done.
For Tubing using extra-short cutting rods and Extra-long tube streching;
These products are out of stock and are available only by special order (custom-made).
Orders and inquiries: Special Tubes Dept. Phone: +81-3-3668-0381
Tapered tube has a thin tip (upper diameter) and a thick base (lower diameter) with a smooth inclination. It can be made into multipurpose cylindrical, square, hexagonal, and octagonal tubes.
Three-roll rolling
Processing
Continuous hydrogen annealing
Dimensional inspection
Product Inspection
Packaging
*Material: Iron-nickel alloy (Invar 36) The Reduction Ratio After Annealing: 45±5%
We have measured and inspected following four dimensions by the automatic checking
machine and sorted out five & NG data which are stored in the PC.
Every single tubing was packed in slotted tray.
We attached every single written data together with the products for traceability.